PhD Defense: Microstructural analysis of atomic mechanisms of metal plasticity under machining conditions: case study of AISI 1045 steel and 7475 aluminum
https://dipc.ehu.eus/en/scientific-activities/joint-seminar-agenda/cic-nanogune/seminar1108
https://dipc.ehu.eus/@@site-logo/dipc-logo.png
PhD Defense: Microstructural analysis of atomic mechanisms of metal plasticity under machining conditions: case study of AISI 1045 steel and 7475 aluminum
CIC nanoGUNE Seminars
- Speaker
-
Bentejui Medina, Electron Microscopy Group
- When
-
2018/07/18
13:00
- Place
- Mondragon University
- Add to calendar
-
iCal
Subscribe to Newsletter
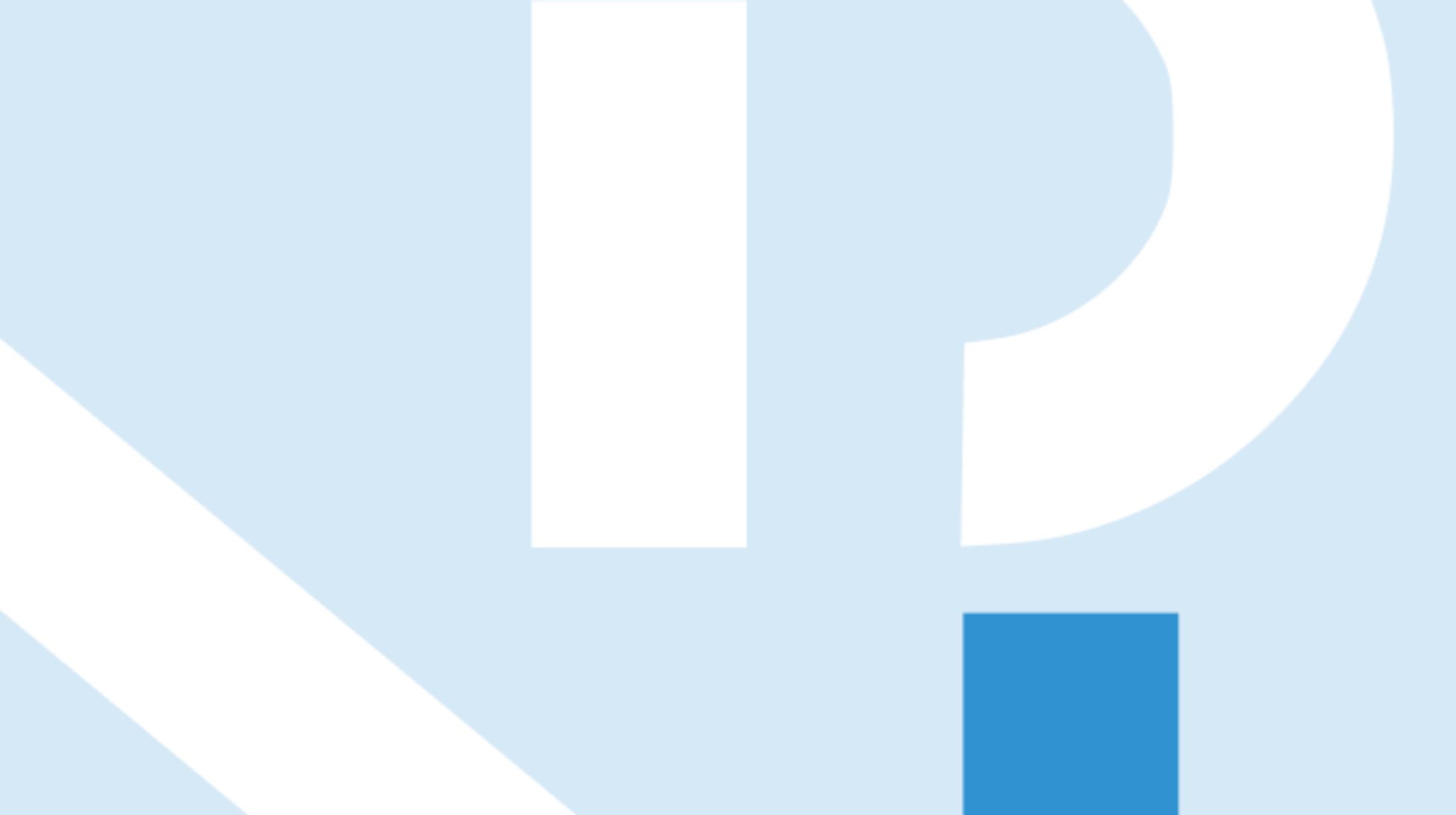
The goal of this PhD thesis is discovering the potential of nanostructure
characterization for revealing atomic mechanisms of metal plasticity under
machining conditions. This approach has been used to reconstruct the phenomena
in the tool-chip contact by a composite study of chips utilizing advanced
microscopy techniques in combination with a fundamental description of
plasticity. There are collected multiple evidences for existence of two
qualitatively different cutting regimes in orthogonal machining of annealed
AISI-1045 steel with uncoated P15 carbide cutting tool in dry conditions at
cutting speed between 5 and 200 m/min. These regimes are characterized by two
different phenomena controlling the tool-chip contact, i.e. severe plastic
hardening at low velocities, and dynamic recrystallization at high speed. This
last phenomenon has induced a structure in the tool-chip contact area with
unique properties. Morphological, chemical and mechanical studies have
revealed a nanostructured material with shifted properties in comparison with
the original material.
The analysis of previously cut chips provides an average picture of the
mechanisms that govern tool-chip contact. However, some aspects like grain
orientation and microstructural features may have differentiated roles. Hence,
the analysis of the cut over individual features could feed a deeper
understanding of metal cutting. In order to address this, the present thesis
studies the potential of direct observation of the machining process in high-
magnification microscopes. For that, a device to perform lineal cutting of
aluminum inside an electron microscope’s vacuum chamber has been designed
and constructed. Based on this device, experiments of machining in-situ have
been successfully performed, shown a coherent chip generation. First results
have shown that the crystallographic orientation may increase the layer of
material deformed under the cutting tool. Furthermore, experiments of cutting
in the sub-micrometer regime has demonstrated that this layer is
proportionally larger in smaller cuts, consequence of a deeper tool-chip
interaction in comparison with macroscopic cutting.
At deeper scales, a method for simulations down to the atomic level has been
proposed to model machining. This initiative relies in the capability of
atomistic simulations to reproduce the mechanisms of plasticity that govern
the deformation of crystalline materials, like dislocations and grain boundary
effects, which cannot be reproduced by other techniques based on continuum
mechanics. In this study a set of molecular dynamics simulations in different
conditions of tool-chip friction and feed size have been carried out. The
results have shown the effects of localized recrystallization observed
experimentally, largely dependent on the friction with the tool. Moreover, it
has been observed that a large friction value reduces the mobility of the
atoms up to certain distance to the tool. This produces a gradient of
velocities in the proximity of the cutting edge, thus supporting the
appearance of specific deformations mechanisms in the area of contact. In
summary, the present work describes the mechanics of machining based on
different atomic mechanisms of plasticity, what has been afforded by
experimental and simulation approaches. In addition, this thesis provides new
methodologies for the research of the cutting process, with potential
application to study other conditions and materials of interest.