Study of machining process in a high-speed linear cutting test bench
CIC nanoGUNE Seminars
- Speaker
-
Cristhian Marcelo Chingo Aimacaña
High-Performance Machining research group at Mondragon Unibertsitatea - When
-
2024/06/10
11:00 - Place
- CIC nanoGUNE Seminar room, Tolosa Hiribidea 76, Donostia-San Sebastian
- Host
- Andrey Chuvilin
- Add to calendar
-
iCal
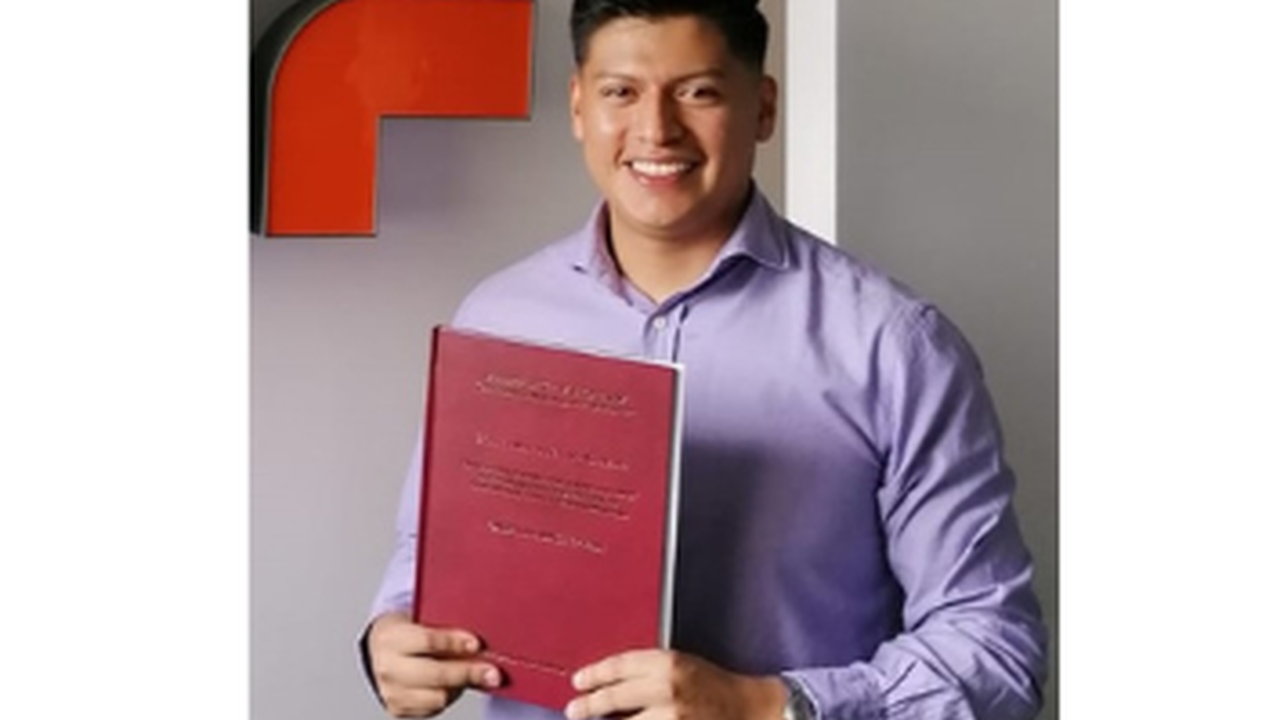
Over the last decades, numerical modeling of orthogonal cutting has continued to dominate research activities. Modeling offers the capability to predict what could happen during the machining process, which when implemented into a process development can reduce or eliminate the need for expensive experimental testing. The fact that results obtained are often uncertain due to uncertainty in the inputs describing the material behavior and tool-chip friction is still a factor limiting the implementation of modeling in the industry. To ensure accurate results, it is crucial to identify the parameters of these inputs under the conditions reached during machining. This task is challenging since the available experimental equipment is not able to reproduce those conditions precisely. As an alternative, inverse simulation has emerged, combining machining tests and numerical modeling to correct parameters. However, this approach may lead to non-unique solution when considering only a fewmachining variables. Therefore, in this thesis we analyze the influence of machining conditions (cutting speed, feed and tool geometry) on the orthogonal cutting process through in-process and synchronous measurement of forces,chip morphology, kinematic (strain, strain rate) and thermal fields. The tests are conducted in a high-speed linear cutting device equipped with a Kistler dynamometer synchronized with a high-speed camera and an infrared camera. The dynamometer measures the three components of force, kinematic fieldsare determined by Digital Image Correlation (DIC) and the thermal fields are obtained from the infrared camera. Additional outcomes such as tool-chip contact length and chip thickness are determined post-process. The experimentally measured machining outcomes will be employed in two main aspects: (i) the inverse identification of parameters related to flow stress, ductile failure and tool-chip friction laws; and (ii) analyzing the influence of machining conditions on the achieved surface integrity in terms of topography, microstructural alterations and residual stresses.
Keywords: Orthogonal cutting, in-process measurement, Digital Image Correlation (DIC), infrared thermography, inverse simulation, surface integrity.